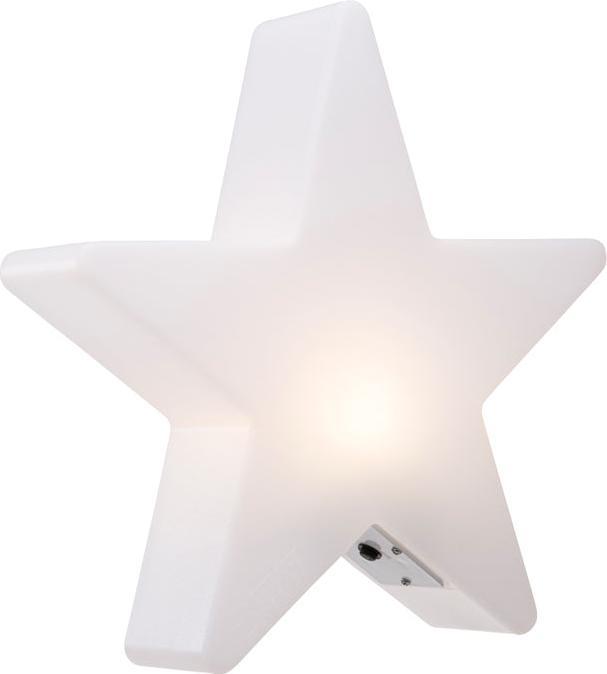
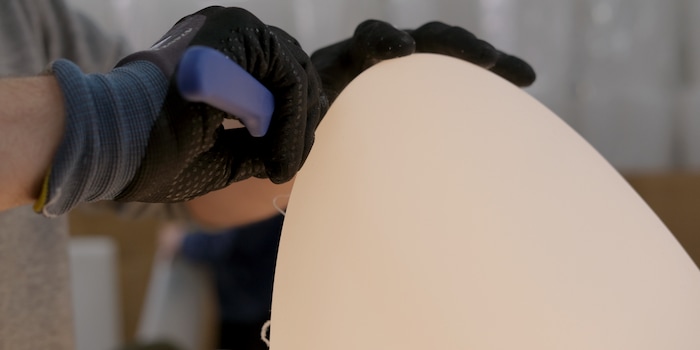
In the limelight: how 8 Seasons Design creates its decorative lamps
Germany-based brand 8 Seasons Design manufactures indoor and outdoor lighting. I paid them a visit to find out what gives their beautiful lamps the edge on the competition.
Although we should be reducing our plastic use, the material is still ubiquitous all over the world. While plastic is proving tough to eliminate, it’s hard to overlook when we think about the future. But what if we were to use it in a way that made plastic products last as long as possible?
8 Seasons Design CEO Tim Lachenmaier and his team are trying to do exactly that. The brand has pioneered the production of weather-resistant polyethylene lamps, and prioritises quality over quantity. In a bid to find out how the lamps are made, I headed to Bremen-Hastedt to visit Tim, originally from Aachen, and his team. Their factory, which they opened in 2017, is right on the River Weser.
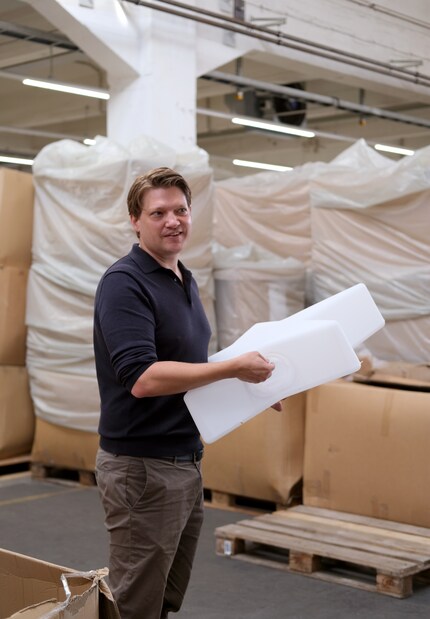
Source: Pia Seidel
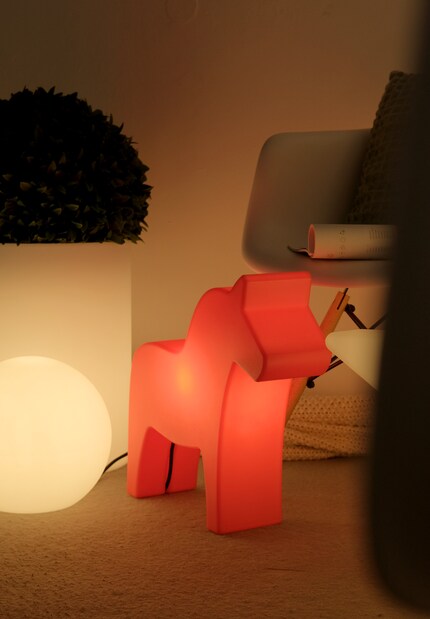
Source: Pia Seidel
Made in Germany
Since launching in 2008, 8 Seasons Design has aimed to manufacture its products locally. Today, 95 per cent of their lamps are produced in Germany: «Using one container of raw material shipped from France, we can produce up to 25 containers of finished products. As opposed to ordering 25 containers from abroad, which would have to be shipped across the ocean,» explains Tim Lachenmaier. The founder’s first ever design, a Christmas star, became a permanent fixture of the brand. It’s their undisputed bestseller – and is a protected design: «The silhouette, as well as the idea of turning a star into a lamp are patented. So whenever you see a design like this, it’s probably come from us.»
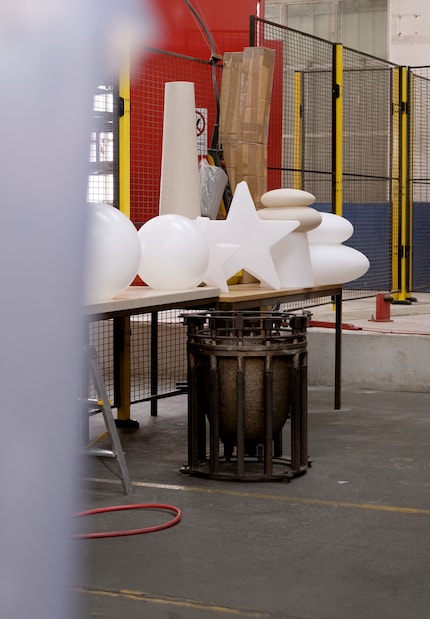
Source: Pia Seidel
Despite the glowing success of the Christmas star, Tim’s thoughts are constantly turning to how the brand’s product range could be expanded. He develops new designs in collaboration with his team and third-party product designers, using trade fairs and, more importantly, the brand’s community, as a source of inspiration. «We use Instagram to find out what kind of response a product might generate,» says Tim. «We ask people about their preferred size or even price.» This way, the team ensures their ideas have market viability before making them a reality. After all, doing so can take up to two years, with prototypes costing a pretty penny. A new rotational mould alone can cost tens of thousands. To find out exactly what makes manufacturing the lighting so expensive, I was given a behind-the-scenes look at the production process.
Breaking the mould
Conventional plastic lamps are produced using an injection moulding process. This involves plastic being pressed into all corners of a mould. Lampshades from 8 Seasons Design, on the other hand, are produced using a rotational moulding process. The technique works exclusively with centrifugal force and boasts a number of advantages, including the ability to create complex, hollow forms all in one go. As the machine rotates at a specific speed and temperature, the plastic is deposited evenly across the two-part mould, keeping all the layers the same thickness. «Compare this to blow moulding, where a drop is distributed from the centre to each corner of the mould,» explains Tim. «If used to make a star, this process would cause the shape to become increasingly thin towards the edges.»
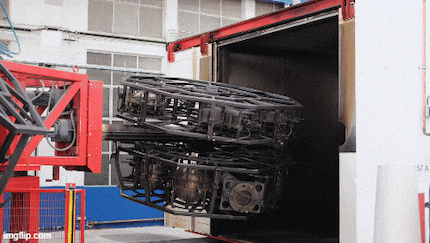
Although it takes longer to manufacture products using this technique, the effort pays off, as there’s only one more step until the finished lampshade. At the point where the two moulds meet, some plastic is left jutting out – similar to what happens with a chocolate bunny or Santa Claus. This can be cut off by hand afterwards.
As well as the manufacturing technique, getting the material right is also crucial in achieving a good outcome. The lamp manufacturer works with pure polyethylene, which is produced in Europe and milled in France and the UK. In contrast to recycled plastics, the fine granules melt more evenly.
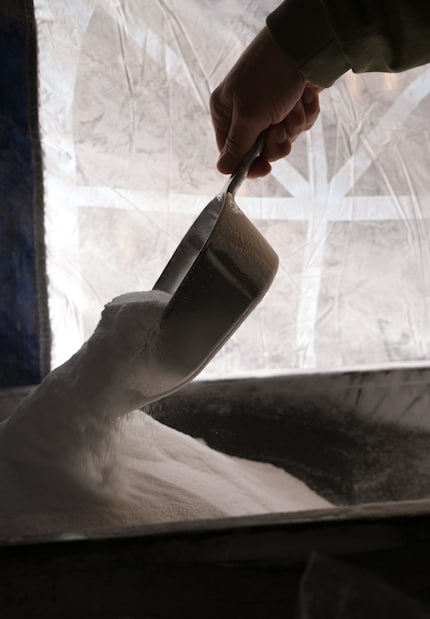
Source: Pia Seidel
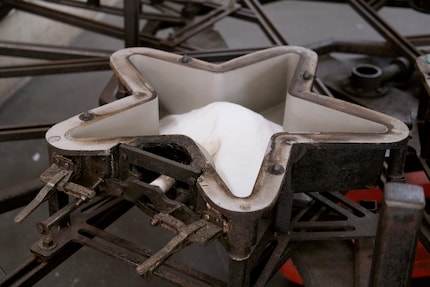
Source: Pia Seidel
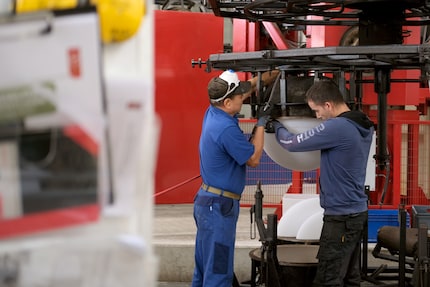
Source: Pia Seidel
To check whether the lamps are completely weatherproof, the team regularly carry out tests in an environmental test chamber located at their sister company, electric motor manufacturer Lloyd Dynamowerke Bremen. This simulates jumps in temperature so that the material’s impact toughness can be determined. To make the plastic more resistant to dirt, 8 Seasons Design also adds UV stabilisers and an antistatic agent to the granulate. Tim explains that other products don’t have this, causing them to become brittle, crumbly and yellowed.
Although the process appears seamless, I wonder if it limits the design possibilities. After all, the shapes are less refined than lampshades made of glass or paper. «There’s a natural limit ensuring that the plastic stops flowing into the corners – and it’s supposed to be that way. If a mould is too narrow, the material can’t get into it and holes end up appearing,» says Tim.
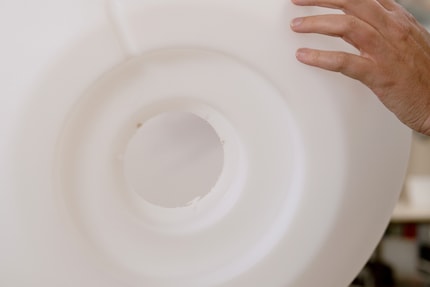
Source: Pia Seidel
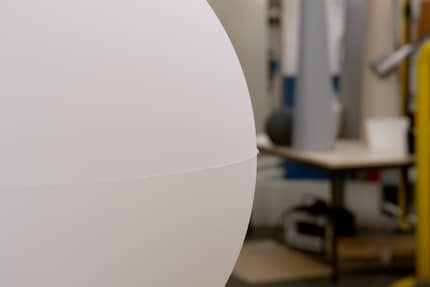
Source: Pia Seidel
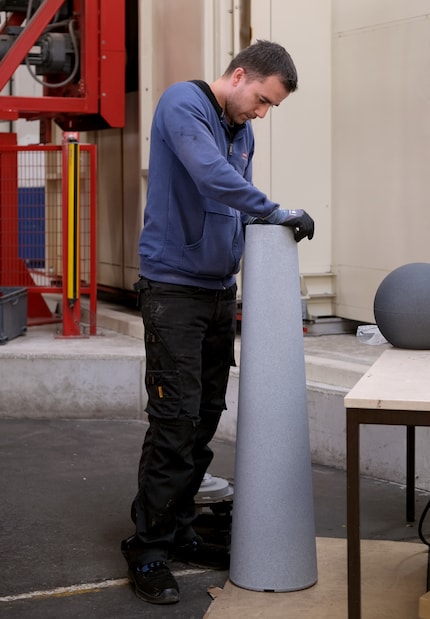
Source: Pia Seidel
Longevity doesn’t come cheap
The brand previously used fixed LEDs. Nowadays, all the lamps have a modular design – even if it does involve a little extra work. As a result, 8 Seasons Design can swap out the individual parts at any time. «We offer customers the possibility to have a solar lamp converted into a wired one and vice versa,» says Tim as he shows me how bulbs are fixed to the shades. If a product gets returned, the advantage of the material 8 Seasons Design uses is that it’s recyclable. «Our mix is particularly popular because it’s clean.»
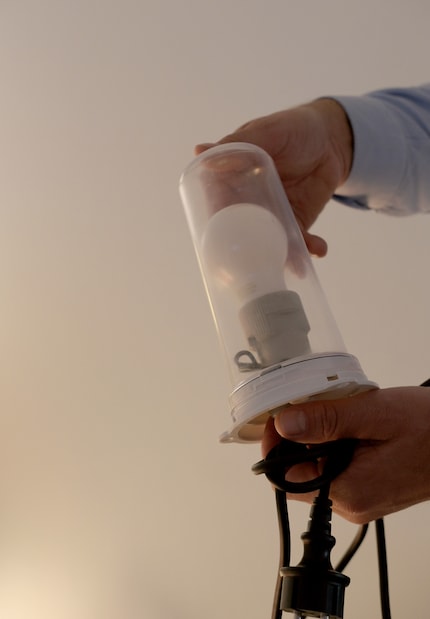
Source: Pia Seidel
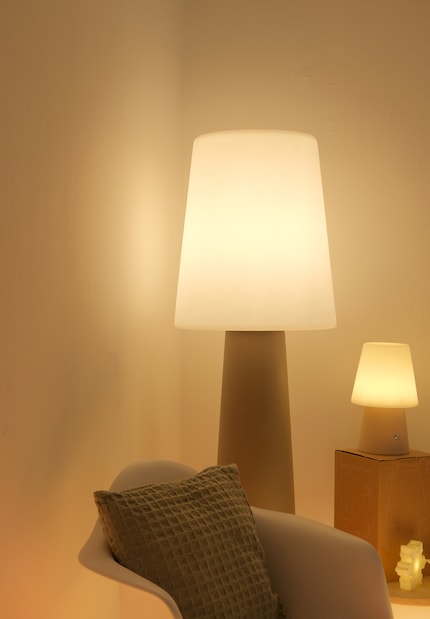
Source: Pia Seidel
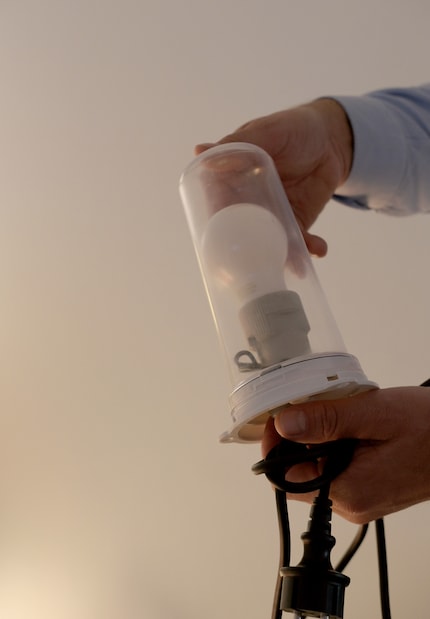
Source: Photo: Pia Seidel
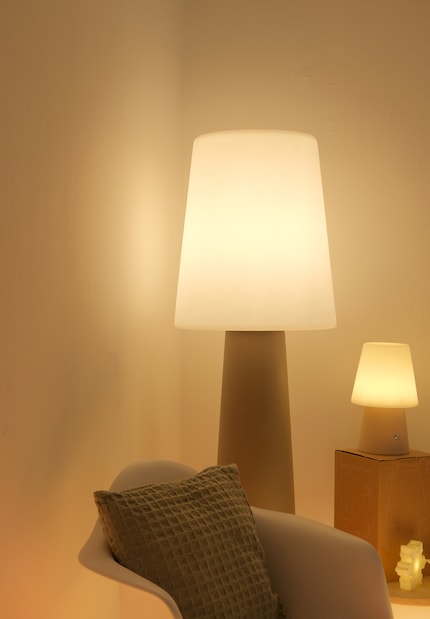
Source: Photo: Pia Seidel
Since 8 Seasons Design uses polyethylene, the company wants to make a conscious effort to keep its ecological footprint as small as possible. At the same time, they’re keen to work on quality. «The fact that we’ve managed to design a timeless product is both a blessing and a curse,» says Tim, preparing to take a break. «If a product’s made to last, you won’t be selling them again and again… but that’s exactly our philosophy.»
Header image: Pia SeidelLike a cheerleader, I love celebrating good design and bringing you closer to everything furniture- and interior design- related. I regularly curate simple yet sophisticated interior ideas, report on trends and interview creative minds about their work.