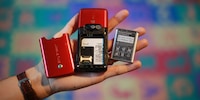
Background information
A mobile's final journey (part 1): how reusable materials are rescued
by Martina Huber
From quicksilver in fluorescent tubes to PCBs in capacitors and flame retardants in plastic – multiple components in old electric and electronic devices containing harmful substances are meticulously removed in cutting plants before the remaining parts end up in the shredder.
Electric toothbrushes, immersion blenders, computers and flat screens, old tube TVs and CD players, coffee machines, battery-powered drills, lamps and devices whose former jobs I can't quite work out: the large hall at the Dock St. Gallen cutting plant is home to wooden pallets full of devices that are broken or no longer wanted. The pallets at the entrance are stacked so high that you can't see what's on them.
Around 165 tonnes of electric and electronic devices are delivered here by truck every month for employees to carry out the disposal of pollutants – the technical term – on behalf of Solenthaler Recycling AG (Sorec). Their task involves removing as many components as possible from the old devices that contain reusable or harmful materials – and they do it by hand.
«Everything that comes in is weighed and sorted first,» explains Markus Stengele, environmental engineer and Head of Quality and Environment at Sorec, who's showing me the cutting plant. Dock St.Gallen is part of Dock-Gruppe and, like many of Switzerland's 80 cutting plants, is a social enterprise of the secondary labour market. Anything that can't be dismantled here is sorted out. This includes devices that can contain oil, such as lawnmowers, chainsaws and additional ovens – they're placed on a separate pallet and the liquid is removed at Sorec before they're shredded in the grinder. Air conditioning and refrigeration units are also sorted out because they can contain cooling agents harmful to the environment. «These have to be siphoned off at a special plant, then we pass them on to a refrigerator recycler,» explains Stengele.
Everything that can be removed with reasonable effort is removed.
The actual work is done on tables inside the hall, where employees take the devices from the pallets, remove batteries where this can be done safely, cut off cables and plugs, open cases and remove reusable materials such as circuit boards or high-quality plastics – and components that are known to contain harmful substances.
«Everything that can be removed with reasonable effort is removed,» explains Heinz Böni, who leads the Critical Materials and Resource Efficiency research group at Swiss Federal Laboratories for Materials Science and Technology (Empa) and has been looking into issues surrounding electric and electronic devices for around 20 years.
According to Böni, the most significant harmful substances that can be found in these devices are still PCBs (short for polychlorinated biphenyls), a group of substances that was used to insulate capacitors and transformers not too long ago. As they're harmful to humans and the environment, do not readily break down and can therefore accumulate in the food chain, they've been banned in Switzerland since 1986. Böni tells me that PCBs aren't much of a problem in new devices, and the number of old devices with capacitors containing PCBs has also reduced considerably. But they're still out there, especially in old radios and sometimes in microwaves or sockets for fluorescent tubes. «PCBs are a problem child, and many of the materials that have replaced them are problematic too,» says Böni. This is why all capacitors measuring 25 mm or above are still removed so that they can be destroyed in a high-temperature incinerator. And yet, if you examine the finely shredded material that comes out of recycling plants, you'll still find traces of PCBs. No-one knows how it gets there.
Quicksilver is another harmful substance that can lurk in our old devices. It's found in the small fluorescent tubes that illuminate first- and second-generation flat screens or the contact switches of some household appliances, such as old washing machines. «Quicksilver is highly toxic and, unlike PCBs, it can't be destroyed,» says Böni. Batrec Industrie AG in Wimmis recovers it from certain kinds of waste, but today it's mostly disposed of in safe, underground disposal sites, like the one in Heilbronn where Swiss materials contaminated with quicksilver end up.
Other relevant pollutants include flame retardants in the plastic of many devices that heat up when they're in use. Take computer, laptop, printer, hairdryer and vacuum cleaner cases for example. «Plastics with flame retardants have to be removed and burned,» says Böni. He tells me that most of the plastics from Swiss waste devices go to MGG Polymers in Austria: «The company is in the position to separate it all cleanly.»
Around 30–40 per cent of plastics are either free of or minimally contaminated with harmful substances that can be remade into new plastic, he adds. As the EU continues to tighten the limit values for different pollutants, however, fewer and fewer of them are allowed to be reused. Recycled plastic is mostly reused in IT and household appliances. According to Böni, a number of large electronics manufacturers use it. «But they don't often communicate it. Because some of them have determined that customers sometimes don't buy devices when they know that they contain recycled plastic. They think that customers will be apprehensive about a drop in quality. Even if it's just a matter of the case.»
The safe removal and destruction of coolants and propellants used in refrigerators and air conditioners is important for the environment. «Many of them are powerful greenhouse gases more than 1,000 times stronger than CO2,» explains Flora Conte. She’s an environmental scientist and Environmental Consulting Project Manager at Carbotech AG, who carries out regular audits of cutting and recycling plants on behalf of take-back systems SENS and Swico. As an auditor, she travels to sites to monitor whether safe storage regulations are being adhered to, materials are being sorted correctly, no reusable materials are being lost and all harmful substances that have to be extracted at the specific cutting plant are being removed. She also checks material flows – how much of a substance goes in and out and in what form and where the individual parts of it end up.
«They do their work to the best of their knowledge and ability,» Conte tells me. «But it's hard to identify and sort everything correctly.» Devices and technology are constantly being further developed, but cutting plant employees also have to know their way around devices that were manufactured 30 or 40 years ago. Take the bulbs from lamps, screens and printers: what contains quicksilver? Where are LEDs already being used? And what still contains old bulbs? «A great deal of know-how is needed to identify and sort everything correctly,» explains Conte. She occasionally sees new information not reaching the corresponding cutting plant from the recycler: «I notice, for example, 'Oh, they haven't been told yet that tumble dryers can also contain heat pumps'.» Sometimes she also uncovers minor sorting errors. These can occur with the different capacitors in washing machines, some of which can be overlooked.
Storing lithium batteries correctly is often an issue. «Lithium batteries, especially defective ones, can cause a fire. If they're missed or end up in the wrong container, things can quickly get dangerous.» Electric and electronic equipment is now less toxic and becoming smaller, welded, and more compact – and harder to recycle. And they contain fewer and fewer batteries, which are sometimes hidden. Because of the arduous removal of harmful substances, correct recycling is also extremely arduous and not profitable, emphasises Conte. Recycling companies receive money from the SENS foundation and manufacturer association Swico in the form of advance recycling fees. «That wouldn't be possible on the free market. Recycling companies would surely remove copper and circuit boards because it makes money. But maybe they'd probably shred the washing machine to get the metal. After all, recyclers don't make a profit from preventing the release of PCBs into the environment. But every kilo of PCBs that can be recovered from old devices is of considerable benefit to the environment.
«Circuit boards never end up in landfill because you can earn money from them,» agrees Markus Stengele from Sorec. «But if I were to send them to India or Pakistan, they might have petrol or waste oil poured over them and be set alight outdoors to burn the plastic. We obviously want to avoid that, so we're regularly monitored and the supervisory authorities want to know exactly where everything's going.» This is why a special permit is required to transport circuit boards from laptops, computers and mobile phones to the smelting plant in Belgium and it has to be renewed every few years. As I walk through the hall of Dock St. Gallen, past pallets full of cut cables, sorted energy-saving and LED lamps, toner cartridges, plastic sheets from screens and other sorted device parts, past two steel containers for batteries that have been removed from all possible devices, I think of my five-year-old daughter's pink wellies, which light up with every step. I didn't think much about it when I bought them; my daughter didn't even want to try on any other model. I won't throw them in my household waste when they’re no longer used. Because somewhere deep inside the soles, firmly glued in so that they don't get wet even when their wearer jumps in deep puddles, there must be small batteries. But when I try to imagine how someone will have to pry the batteries out, I ask myself whether buying these wellies was a smart decision. Do they really have to light up?
And this makes me think about what Flora Conte said in our phone conversation. «Recycling is done very well in Switzerland. Our main problem isn't technology; it's our high level of consumption. The many devices that we use, all of the raw materials that have to be extracted. This is where the big environmental impact is – even if we recycle perfectly.» As part of her work, she's had to get used to seeing devices that still look new and could definitely have been used for longer all the time. The next three instalments of the series will address issues including how old devices are dealt with in other parts of the world, the problematic mining of raw materials and rare earth elements in them and why we should use our devices for as long as possible before we dispose of them correctly.
Missed part 1? You can read it here and find out how much work it takes to remove a battery from an old smartphone.
As a freelance science journalist, I enjoy writing in-depth stories on health, environment and science.