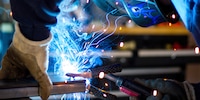
Background information
Learning to weld: big ideas, no skills
by Carolin Teufelberger
I've already done a lot with wood. Now it's time for metal. I want to learn how to weld so that I can build my own furniture. Step 2: attending the course.
The day has arrived: my welding course is taking place today. I would describe my state of mind as joyfully nervous. Will I be able to do everything? And what kind of people will be there? I find out at 12 o'clock. Wearing a thick jacket and sturdy leather shoes, I walk briskly along the Limmat to the Jugendkulturhaus Dynamo. I've forgotten my mask at home and had to get a disposable model from the Migrolino petrol station shop as an emergency, which is why I'm slightly behind schedule.
Seven other people want to practise metalworking. At the moment, no more are allowed to take part in the course. The group is diverse, ranging from young to a little older, from totally inexperienced to semi-professional. The project ideas range from firewood storage solutions and table legs to a drip tray for your own beer tap. My black plate shelving system idea seems to require a rather high amount of materials in comparison, but I'm not letting that discourage me. Theory is the order of the day to start with.
The course instructor, a qualified metalworker, shows us the machinery: the sheet metal shears, the roll bending machine, the folding machine, the sandblaster, the plasma cutter, the band saw and the belt sander. At each station, a few volunteers are allowed to try out the machine. Questions are always allowed. This opportunity is actively used, even for hypothetical scenarios such as bending a pipe with a diameter of eight metres. If a sewerage system is to be laid as a hobby, I assume. From time to time, my impatience and short attention span become apparent. I'm more of a "trial and error" kind of person; hours of theory challenge me. Nevertheless, I realise how important it is, so I listen, work my legs to the bone and drink a cappuccino during the short break until it's finally my turn to weld.
At first glance, the welding machine reminds me of a balloon artist's helium machine. Instead of cute animals, there's retina-burning light, electricity and inert gas. Even the mere words instil me with respect. The instructor shows us perfect, good and bad seams. Then it's our turn. Let's see if I've been paying attention.
The current is running, the shielding gas is on, the negative terminal is fixed to the metal table. The welding rod, which emerges from the nozzle at a fixed speed, acts as the positive pole. This means that the circuit is only closed when the wire touches the metal to be welded. If I pull the trigger of the welder anywhere in the air, more wire simply emerges. I put on a hard hat with a visor that darkens automatically. This allows me to see where I'm applying the welder. I place the nozzle with the protruding wire on the piece of sheet metal at a 45-degree angle. Then I have to hold my breath, otherwise the seam will be uneven. It will be anyway. I get caught on the metal sheet a few times, which has the same effect as raising and lowering the rib cage. I also pull the device far too quickly, so that too little material is piled up.
But I am capable of learning and so my stitches are getting better and better. I'm even trying my hand at a fillet weld, i.e. a welded joint at a 90-degree angle, which is a little more challenging to execute. I feel more and more confident and really enjoy the work. I show the instructor my shelf idea in detail to pick up some valuable tips. I'm pleased with my decision, as he first tells me that the individual shelves will weigh over 50 kilograms. I had completely underestimated the weight of three millimetre thick sheet steel. He advises me not to weld the shelves permanently, but only to attach brackets on which I can place the black sheet metal panels. That seems sensible to me for transport and future moves. Nevertheless, I'm waiting to order the material to think everything through again. I'm very hesitant when it comes to buying or building furniture and I have to be completely convinced of the design.
So I practise a little more and discuss with the other participants until the six hours are up. I've learnt a lot about metalworking today, got to grips with a lot of unfamiliar machines and observed the behaviour of thin steel. I realise that I need to come back soon and work independently in the workshop so that I don't forget all of this straight away, but internalise it. Probably with occasional help from the supervisors.
In the next step, I order cut-to-size black sheet metal and start on my first shelf. Then there will be sanding, welding and most likely a bit of swearing.
My life in a nutshell? On a quest to broaden my horizon. I love discovering and learning new skills and I see a chance to experience something new in everything – be it travelling, reading, cooking, movies or DIY.