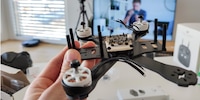
Hintergrund
Drohne die Erste - Ach du verbranntes Ding
von Manuel Wenk
Ich muss für die DIY-Racing-Drohne von Kollege Manuel eine Halterung per 3D-Druck herstellen. Nicht ganz einfach, da wir nur digital kommunizieren können. Fehler sind programmiert.
Der Bau der eigenen Racing-Drohne hat für Manuel holprig begonnen. Bereits nach kurzer Zeit hat er das Teil in Brand gesteckt. Und nun sitzt er vor dem nächsten Problem: Die Kamera und die Antennen brauchen eine Halterung, sonst lassen sie sich nicht befestigen. Eine, die man nicht kaufen kann, sondern selber basteln muss.
Glücklicherweise habe ich den PlaySmart 3D-Drucker von Polaroid zum Testen – mein privater Drucker ist wieder mal in Reparatur. Gemeinsam suchen Manuel und ich auf Thingiverse nach passenden Teilen. Nach einer Weile glauben wir, die passenden Halterungen gefunden zu haben. Für die Kamera nehmen wir dieses Teil und für die Antennen dieses.. Ich drucke die Teile und schicke sie ihm per Post.
Die Kamerahalterung passt, Manuel muss jedoch die Löcher etwas ausbohren. Die Antennenhalterung hingegen passen nicht. Der Abstand zwischen den beiden Befestigungsschrauben ist nicht gross genug. Er kann das Teil nicht anschrauben. Wir müssen uns etwas anderes einfallen lassen. Ich schlage Manuel vor, dass ich ihm das Teil massgetreu mit CAD konstruiere und dann drucke. Es beginnt ein Hin und Her mit digitaler Kommunikation der guten alten Post.
Wir treffen uns zu einer Teams-Konferenz. Dieses Mal machen wir gleich von Beginn weg alles richtig – denken wir zumindest. Wir sprechen ab, was Manuel vermessen muss, damit ich die korrekten Masse für mein CAD-Programm Fusion 360 habe. Obwohl die Halterung nicht sonderlich komplex ist, wird das für mich eine Herausforderung. Bis jetzt habe ich nur sehr simple Sachen konstruiert.
Beim Design der Halterung orientieren wir uns an der Vorlage von Thingiverse, die nicht gepasst hat. Was Manuel dabei noch aufgefallen ist: Die Röhren für die Antennen sind viel zu lang. Sie sollten kürzer sein, damit die Antennenkabel auch lang genug sind, um sie mit dem Gehirn des Quadcopters zu verbinden. Mit den korrekten Massen mache ich mich an die Arbeit.
Das Schwierigste ist für mich, das Rohr für die untere Antenne in einem 60-Grad-Winkel zur oberen Antenne zu konstruieren. So etwas habe ich bis jetzt noch nicht gemacht. Es gelingt mir zwar, aber der Querschnitt des Rohrs verwandelt sich dadurch von einem Kreis zu einer Ellipse. Das ist in diesem Fall nicht schlimm, das Loch im Rohr ist immer noch breit genug, damit Manuel die Antennenkabel durchziehen kann. Nach etwa vier Stunden Arbeit bin ich fertig. Ich schicke ihm das Design per Teams und wir besprechen erneut per Videokonferenz.
Er schaut sich mein Design als 3D-Modell am PC an und vergleicht es mit dem Teil, das ich ihm bereits gedruckt habe. Da fällt ihm etwas auf: Die Antennenhalterung, die nach oben zeigt, stösst am Quadcopter-Gerüst an. Er kann die Halterung so nicht gebrauchen. Bei seinem Quadcopter muss eine Antennenhalterung nach vorne zeigen und eine nach unten.
Ich muss nochmal über die Bücher. Damit die Halterung kompatibel ist, müssen beide Antennenhalterungen gegen vorne rauskommen. Was zuvor noch kein Problem war, wird jetzt eines: Weil die obere Halterung nun gegen vorne schaut und nicht mehr gegen oben, muss ich den Winkel der unteren Halterung weiter gegen unten richten. So wird der elliptische Zylinder enorm schmal. Es lässt sich nur noch ein kleines Loch rein konstruieren, durch das die Antennenkabel müssen. Wir sind nicht sicher, ob die Kabel da überhaupt durchpassen. Ich gehe bei den Wanddimensionen an die Grenzen und konstruiere sie enorm dünn. Wir entscheiden uns, das Teil mal so zu drucken.
Die Grenzen des Möglichen mit dem 3D-Drucker haben wir überschritten: Auf den äusseren Seiten des elliptischen Rohrs haben sich beim Druck Risse gebildet. Das Teil hält trotzdem und ich schicke es Manuel per Post.
Das Problem mit dem elliptischen Rohr lässt mir keine Ruhe. Es kann nicht sein, dass es keine andere Möglichkeit gibt. Da ich sowieso vergessen habe mein Projekt zu speichern ...
… setze ich mich nochmal an Fusion 360. Vier Stunden Arbeit für nichts. Davon lasse ich mich nicht aus der Ruhe bringen und dank der Erfahrung vom Vortag ist das Teil innert Kürze rekonstruiert – dieses Mal sogar besser. Ich entdecke nämlich eine Funktion, die es mir ermöglicht, den Zylinder tatsächlich in zylindrischer Form zu erstellen. Ich drucke das Teil und schicke es per Post.
Manuel versucht die Halterung zu montieren. Gleich mehrere Dinge passen nicht. Erstens ist der Abstand zwischen den Löchern zur Befestigung am Quadcopter zu gross. Er müsste wieder ausbohren. Zweitens sind die Antennenrohre immer noch zu lang. Die Kabel kann er so nicht mit dem Gehirn der Drohne verbinden. Drittens sind die Ausbuchtungen für die Antennenköpfe, dort wo die Sende- und Empfangseinheit sitzt, zu tief. Die Köpfe verschwinden komplett darin, was sie nicht sollten. Und viertens: Er hat die Höhe der Halterung falsch gemessen. Sie muss einen Zentimeter kürzer sein. Ich muss das Modell nochmals überarbeiten.
Die Anpassungen sind schnell gemacht und da mittlerweile mein CR-10S Pro wieder in Betrieb ist, drucke ich das Teil mit meinem Drucker. Ein neues Paket geht auf die Post. Mittlerweile kann ich Manuels Adresse auswendig.
«Auch das noch!» schreibt mir Manuel per WhatsApp. Mist, was passt jetzt wieder nicht? Kurz darauf folgt ein Bild.
Hmm… Die Antennenkabel passen. Wo liegt das Problem? Die Erklärung: Er musste das Kabel zum Verbinden derart biegen, dass das Verbindungsstück abgebrochen ist. Mit dem gedruckten Teil ist sonst alles in Ordnung. Es passt perfekt.
Wir besprechen die Lage kurz per Teams. Er bestellt neue Antennen und ich fertige das Teil erneut. Dieses Mal vergrössere ich den Ausgang für die Kabel und runde ihn zusätzlich ab. So lassen sich die Antennenkabel besser führen.
Meine Arbeit ist erledigt – und ich auch. Prototypen auf Distanz und ohne Erfahrung ist echt mühsam. Dennoch: Ich bin stolz, dass das Teil endlich passt und ich Manuel helfen konnte.
Technologie und Gesellschaft faszinieren mich. Die beiden zu kombinieren und aus unterschiedlichen Blickwinkeln zu betrachten, ist meine Leidenschaft.