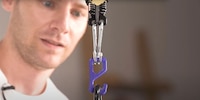
Produkttest
Das Günstigste gehört zu den Stärksten: PLA-Vergleichstest Teil 2
von Kevin Hofer
Der Infill, also der prozentuale Anteil der Füllung eines 3D-Drucks, hat Einfluss auf die Stärke des 3D-Drucks. Wie sich der Infill auf die Zugkraft auswirkt, habe ich getestet.
Was habt ihr mich bei meinem letzten Test kritisiert…
Junge, Junge! Wie kann man nur so leichtsinnig sein... Schütze DEINE AUGEN!!!
Wäre das eine Arbeit eines Lehrlings aus unserer Werkstätte, hätte es dafür in jedem Fall ungenügend gegeben und dann noch einen saftigen ZS bezüglich Arbeitssicherheit.
Danke für die zahlreichen Rückmeldungen auf diesen Artikel:
Bei der Kritik zur Arbeitssicherheit habt ihr es aber nicht belassen. Derselbe Anonymous wie oben wirft mir fragwürdigen Inhalt vor:
Zu meiner Verteidigung: 3D-Drucken ist für mich ein Hobby, darüber zu schreiben konnte ich zu einem Teil meines Berufs machen. Ich bin also eher ambitionierter Amateur als nachlässiger Profi und lerne ständig dazu. Kein Grund also für einen Zusammenschiss oder «ZS», wie das Anonymous im Militärjargon bezeichnet.
Gut, dass User sfluck einen Beitrag zum Einfluss von Infill, Wand- und Schichtdicke auf die Zugkraft postet. Das will ich selbst ausprobieren, dabei meine Testmethode verbessern und mehr Informationen zum Verfahren geben. Zuerst zum Druckverfahren. Ich erstelle jeweils drei Drucke der Test-Haken mit 0, 10, 20, 30, 40, 50, 60, 70, 80, 90 und 100 Prozent Infill. Die Haken drucke ich liegend, 15° diagonal zur X-Achse. Ich drucke leicht diagonal, weil ich bei meinem Creality CR-10S Pro festgestellt habe, dass die Modelle so besser auf der Bauplatte haften. Die weiteren Einstellungen in Cura in Englisch:
Hier gibt es Änderungen im Vergleich zum letzten Test. Dort habe ich mit 1.5 Millimeter Wanddicke (Wall Thickness) dickere Wände gedruckt. Die Schichthöhe (Layer Height) war mit 0.15 niedriger, das heisst, dass ich beim letzten Mal mehr Schichten gedruckt habe. Dafür ist die Dicke der Ober- und Unterseite (Top/Bottom Thickness) mit 1.12 Millimeter grösser. Diese Faktoren haben ebenfalls Einfluss darauf, wie viel Zugkraft der Druck aushält. Dazu mache ich in Zukunft weitere Tests. Jetzt geht es mir darum, den Einfluss des Infills zu testen und den optimalen Anteil für die weiteren Tests zu finden.
Beim ersten Versuch habe ich andere Einstellungen gewählt, weil ich mich am PLA mit Carbonfasern von Proto-Pasta orientiert habe. Mit diesem Filament hatte ich beim ersten Test der Reihe Mühe beim Drucken. Da ich dieses Mal nur mit dem Filament von Purefill teste, kann ich die Standardeinstellungen von Cura bei 0.28 Millimeter Schichtdicke wählen. So geht das Drucken schnell.
Den Test mache ich mit dem Purefill-Filament, das im Test am besten abgeschnitten hat. Ich hole mir eine neue Spule, um Alterungsprozesse, Feuchtigkeit oder ähnliche Abnutzungserscheinungen auszuschliessen. Dieses Mal bin ich zu Hause. Hier ist es während dem Test zwischen 25.7° Celsius und 26.1° Celsius warm. Im Studio, wo ich den letzten Test gemacht habe, ist es das ganze Jahr über zwischen 18° und 20° Celsius.
Das Drucken der einzelnen Modelle dauert zwischen 1:13 Stunden und 2:25 Stunden. Wobei sich pro 10 Prozent mehr Infill die Druckzeit bis 90 Prozent Infill um durchschnittlich 5 Minuten erhöht. Von 90 Prozent Infill auf 100 verlängert sich die Druckzeit dann exponentiell um 28 Minuten von 1:57 auf 2:25 Stunden. Das verwendete Druckmaterial erhöht sich pro 10 Prozent mehr Infill von 12 Gramm bei 0 Prozent Infill auf 23 Gramm bei 100 Prozent Infill. Nachdem ich alle Haken gedruckt habe, lasse ich sie 24 Stunden auskühlen und mache mich danach gleich ans Testen.
Mir ist bewusst, dass mein Test nicht wissenschaftlichen Kriterien genügt. Ich teste schliesslich nicht im Testlabor und kann aufgrund des Testverfahrens mit der Gewichtsweste nur in 1,5 Kilogramm-Schritten erhöhen. Auch sonst gibt es Faktoren, die den Test beeinflussen. Beispielsweise die Qualität des Filaments. Da gibt es ja, wie ich beim ersten Test festgestellt habe, Unterschiede. Der Test richtet sich auch nicht an professionelle 3D-Drucker, die Drucke für die Industrie herstellen, sondern an private Maker wie mich, die Freude am Ausprobieren und Tüfteln haben.
Beim Ausführen des Tests orientiere ich mich beim Vorgehen vom letzten Mal. Ich hänge meine Gewichtsweste an die Haken, bepackt mit unterschiedlichen Gewichten. Ich taste mich in Anderthalb-Kilogramm-Schritten – so viel wiegt ein Sandpack der Gewichtsweste – an die Gewichtsgrenze der einzelnen Haken heran. Wenn ich die Gewichtsweste immer wieder an- und abhänge, wird das Material jeweils gestresst. Es kann sein, dass der Haken noch mehr Gewicht aushalten müsste. Deshalb drucke ich drei Haken mit derselben Infill-Einstellung. So nähere ich mich dem Maximalgewicht und kann im Idealfall alle drei Haken mit demselben Höchstgewicht beladen. Ich starte mit 15 Kilogramm Sand in der Weste.
Ach ja: Noch etwas ist neu.
Ich trage jetzt Brille. Damit der Boden meiner Mietwohnung durch den Fall der Weste nicht beschädigt wird, lege ich mein Balance-Pad unter die Klimmzugstange/Fingerboard-Combo, an der ich das Ganze befestige.
Bei meinem letzten Test hat das Purefill-Filament mit 10 Prozent Infill 22,5 Kilogramm Zugkraft ausgehalten. Davon ist das Filament dieses Mal mit 16,5 Kilogramm weit entfernt. Das liegt an den angepassten Parametern (siehe oben).
Hier die Ergebnisse:
Infill in Prozent | Erreichtes Gewicht in Kilogramm | Druckzeit in Stunden und Minuten | Verwendetes Filament in Gramm |
---|---|---|---|
0 | 15 | 1:13 | 12 |
10 | 16,5 | 1:21 | 13 |
20 | 18 | 1:25 | 14 |
30 | 19,5 | 1:30 | 15 |
40 | 21 | 1:34 | 16 |
50 | 22,5 | 1:38 | 18 |
60 | 22,5 | 1:45 | 19 |
70 | 24 | 1:49 | 20 |
80 | 25,5 | 1:53 | 21 |
90 | 27 | 1:57 | 22 |
100 | 27 | 2:25 | 23 |
Anhand der Ergebnisse lassen sich zwei Infill-Einstellungen ausschliessen die keinen Vorteil gegenüber weniger Infill haben. Bei 60 und 100 Prozent Infill haben die Testhaken nicht mehr Zugkraft ausgehalten als bei 50 respektive 90 Prozent. Bei 100 Prozent Infill ist zudem die Druckzeit exponentiell länger, weshalb ich 100 Prozent Infill beim Drucken nicht empfehlen würde.
Aufgrund dieser Resultate werde ich künftig bei den meisten meiner Drucke, die Zugkraft aushalten müssen, auf 50 Prozent Infill zurückgreifen. Muss es noch mehr sein, werde ich wohl auf 80 Prozent Infill erhöhen.
Wie ich beim letzten Mal herausgefunden habe, ist das Filament dabei entscheidend, wie viel Zugkraft es tatsächlich aushält. Ein anderes PLA-Filament würde eventuell mehr oder weniger Zugkraft bedeuten. Dennoch erkenne ich eine gewisse Tendenz, bei wie viel Infill mehr Zugkraft resultiert. Bevor ihr mir wieder die Kommentarspalte zu spammed: Ich weiss, universell anwendbar sind diese Ergebnisse nicht.
Jetzt, wo ich den für mich optimalen, prozentualen Anteil an Infill ermittelt habe, teste ich den Einfluss der Wanddicke auf die Zugkraft bei 50 Prozent Infill.
Habt ihr weitere Anregungen zum Testverfahren? Dann schreibt eure Tipps in die Kommentarspalte.
Technologie und Gesellschaft faszinieren mich. Die beiden zu kombinieren und aus unterschiedlichen Blickwinkeln zu betrachten, ist meine Leidenschaft.